HUNDÅ LOST WAX BRONZE DAYBED
The idea for this project came from my introduction to Tanner Boyes, who had helped another furniture designer create a complex curved aluminum lounge collection. Tanner had equipment and tooling that were rare and connections to a foundry in Springville, Utah, that creates Lost Wax casts for bronze sculptures. I knew the piece I wanted to create was unique in form, also complex in curvature. As I explored my fabrication options, it made the most sense to try to create this daybed in a foundry. The shape of the daybed occurred to me during my solo trip to Boulder, Utah, where I went to find inspiration of form from the red rocks that had been carved from thousands of years of water and wind. I laid my body on the rock formations, studying form in relation to my body. I sketched the original form of the bronze daybed in the desert in June 2023. The initial form was easy to develop, inspired by nature. But the complexity of the process taught me how to communicate in terms of technical furniture engineering and how to be a sculptor of plaster and bronze.
A piece with this amount of complexity in form needed to be rendered digitally first to ensure it had the engineering to hold the weight of itself and the upholstered portion attached. Once the shape resembled what I had originally sketched in the desert—a 3D print of it was created. This print was just a skeleton to the final form intended. I added layers of Bondo and Plaster of Paris to the 3D print, sanding after each layer to sculpt the shape as it felt right. It was important to not cover the plastered piece in wax before it entered the molding process, which is a typical first step to blend out any imperfections. I wanted to keep the natural texture of the plaster—some of the parts that came to the surface from sanding, the brush strokes, and organic edges. The form took a lot of its shape on its own—how the plaster laid on the surface and what I felt right to subtract from the form in the sanding process. After the plaster piece was molded, it went through the complex Lost Wax process of waxing, spruing, ceramic shelling, de-waxing, firing, casting, then de-shelling. Tanner and I moved the pieces to his shop each end was cut into four sections. Tanner welded the four sections together. I ground down the left over spruing, welds, and imperfections of the piece. There were parts of the original shape that needed to be adapted—more grinding and sanding were needed to achieve the desire final shape. This began the bronze sculpting process which started to inform the final shape this piece would take. The bronze piece then went through a multi-step process of sanding from low to highest sandpaper grit to create a high-polish piece. A Scotch Brite pad was used as the final step to take it back one luster from a mirrored finish.
The pieces were shipped to Italy to complete the custom frame and upholstery. The cushion was made from a spring-like high-density foam and down. The pillows filled with down have fabric attached that fall through the top opening and are held with a bronze spiral weight that I carved from clay and cast in bronze at Tanner’s shop. The fabric chosen for this piece is a deep red-brown wool satin from Dedar that represents the deepest color of the red rocks.
2023-2024
High-Polish Cast Natural Bronze,
Dedar Satin Wool, Plywood Frame,
High-Density Foam and Down Cushion
2286 mm x 889 mm x 787 mm
177 kg
Produced by Emily Thurman in Utah
Upholstered in Italy
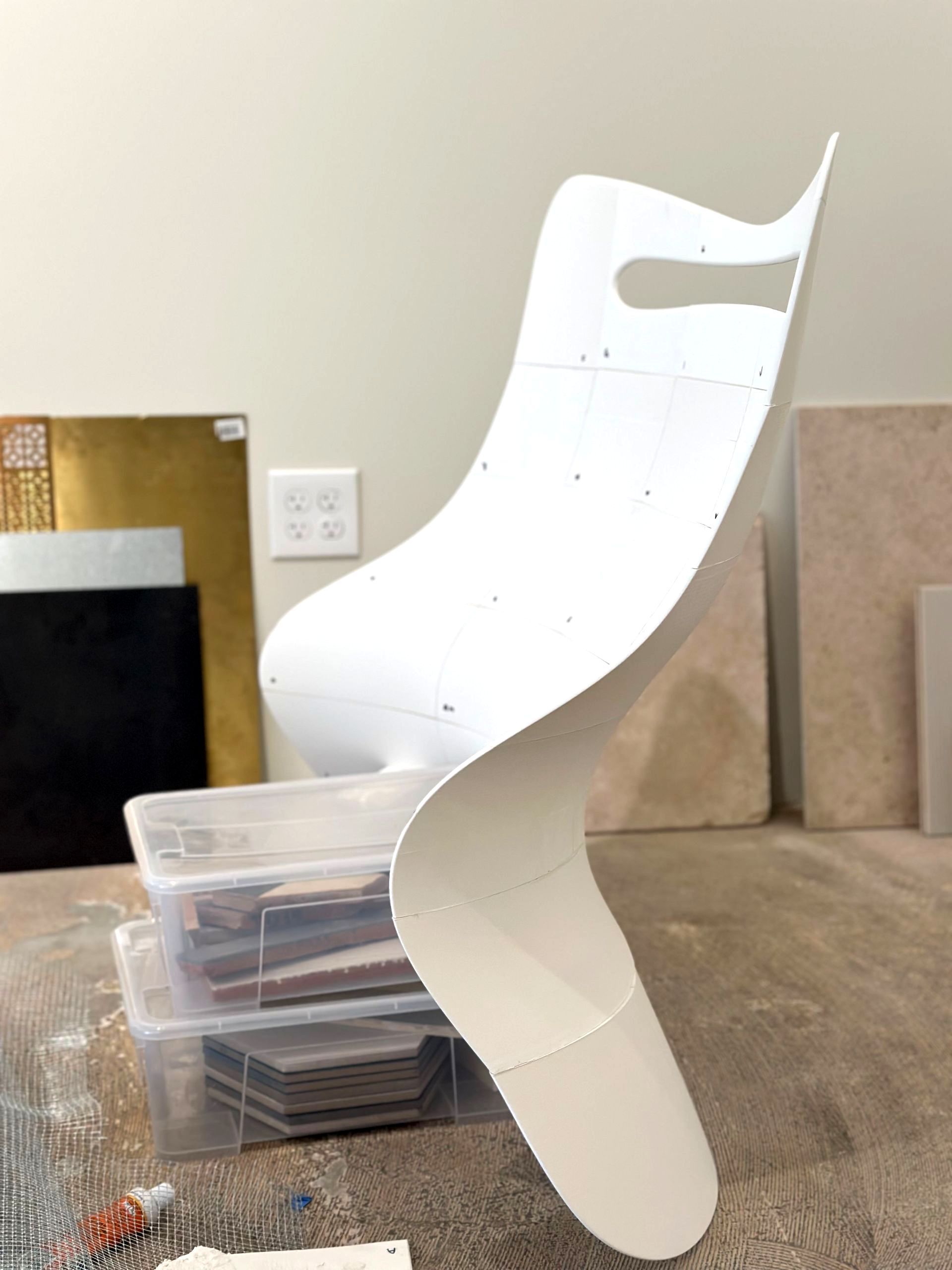